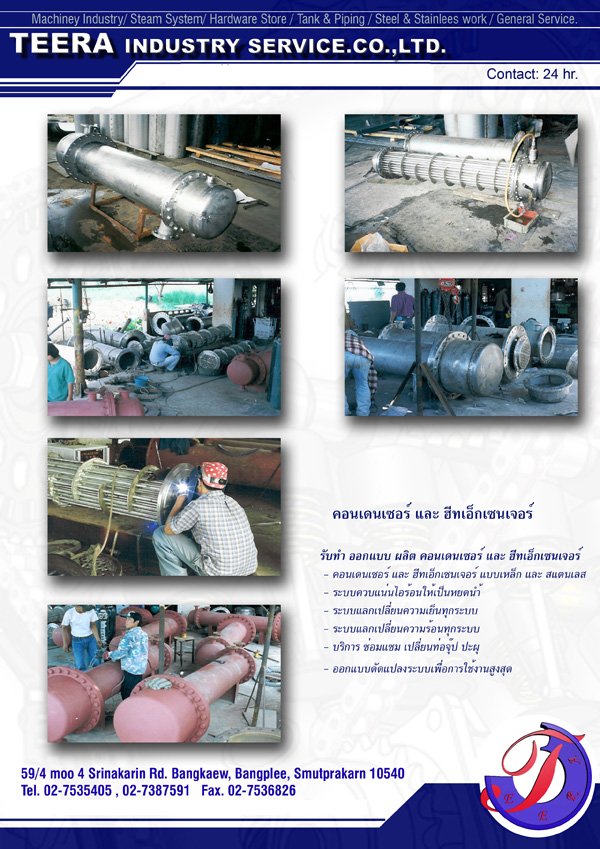
Specifications
Tube heat exchanger
- High efficiency heat exchanger
- Based on customer's requirement
- Shell & Tube Heat Exchangers
Tube heat exchanger
Introduce
High heat exchange speed, high temperature resistance (400°C) and high pressure resistance(2.5MPa); High efficiency and energy conservation: The heat transfer coefficient reaches
3000-4000W/m2.°C in the transfer from steam to water and 2000-3500 W/m2.°C in the transfer from water to water.
Structure design: --Tube type
§ Tube diameter: Using a small tube diameter makes the heat exchanger both economical and compact. However, it is more likely for the heat exchanger to foul up faster and the small size makes mechanical cleaning of the fouling difficult. To prevail over the fouling and cleaning problems, larger tube diameters can be used. Thus to determine the tube diameter, the available space, cost and the fouling nature of the fluids must be considered.
§ Tube thickness: The thickness of the wall of the tubes is usually determined to ensure:
§ There is enough room for corrosion
§ That flow-induced vibration has resistance
§ Axial strength
§ Availability of spare parts
§ Hoop strength (to withstand internal tube pressure)
§ Buckling strength (to withstand overpressure in the shell)
Heat transfer tube:
1) Pure seamless titanium tube . Thickness2 mm. The Grade is TA1.
2) The tube pressure loading capacity was designed base R410a high pressure work condition, The max. working pressure is 52 bar. and the extreme pressure was 360bar in our test.
3) 100,000 times alternating pressure (Low pressure 0 bar, high pressure 52bar) test shows it can be used more than 20 years. Never corrosion.
Specification:
1) The data marked by orange is this model heat exchanger technical parameter. Please contact us to get the detail drawing.
2) The data list is our suggested data, We can produce any capacity heat exchangers according customer requirement and design.
Model type | Capacity | Size |
10 sq. m HE | 20 Kw | Shell SA-516/70 ID 200 TBD mm. |
50 sq. m HE | 70 Kw | Shell SA-516/70 ID 300 TBD mm.
|
100 sq. m HE | 150 Kw | Shell SA-516/70 ID300 TBD mm.
|
150 sq. m HE | 200 Kw | Shell SA-516/70 ID 400 TBD mm. |
200 sq. m HE | 270 Kw | Shell SA-516/70 I400 TBD mm. |
250 sq. m HE | 380 Kw | Shell SA-516/70 ID 400 TBD mm. |
300 sq. m HE | 420 Kw | Shell SA-516/70 ID 600 TBD mm. |
350 sq. m HE | 530 Kw | Shell SA-516/70 ID 1600 OD : TBD mm.
|
400 sq. m HE | 620 Kw | Shell SA-516/70 ID600 TBD mm. |
500 sq. m HE | 740 Kw | Shell SA-516/70 ID 600 TBD mm. |
800 sq. m HE | 970 Kw | Shell SA-516/70 ID 800 TBD mm. |
1,000 sq. m HE | 1600 Kw | Shell SA-516/70 ID 800 TBD mm. |
Heat Exchange Concepts & Heat Exchangers
Heat Exchanger Fundamentals
Heat exchange is a natural phenomenon occurring throughout our environment. It drives the weather cycles and energy exchange between ecosystems. Harnessing its utility through accurate control of heat exchange has been a focus of our industry for over a century.
Heat exchangers allow control over the dynamics of heat transfer between fluids. They are used in widespread applications, such as solar heating, pool heating, domestic water heating, radiant floor heating, food processing, marine applications, general industrial process control, and more.
Below are parametric thermodynamic equations that define the nature of heat exchange and performance of a heat exchanger for any given application. Once these thermal parameters are determined they can be used to calculate heat exchanger performance in order to select the most suitable product based on the specific application.
Theoretical Heat of a Fluid
The heat transfer principal in heat exchangers is based on a colder fluid gaining heat from a relatively hotter fluid separated by, and flowing over, a heat conductive material.
This is expressed by the following formula:
Heat exchanger equation1 (eqn 1)
Q = Total heat load
m = Mass flow rate of fluid.
cp = Specific heat of fluid at constant pressure.
DT = Change in temperature of the fluid.
This formula provides the Theoretical Heat Yield to or from a given fluid undergoing a temperature change, DT at a mass flow rate, m with the fluid’s specific heat property, cp.
Practical Heat Transfer Control
The theoretical heat yield of a fluid gives the amount of heat that needs to be transferred into or from a fluid. The practical heat transfer is a function of the physical geometry of the heat exchanger, its material composition, and the fluid condition.
The general form of the equation defining the maximum potential heat transfer through a heat exchanger is expressed by the formula:
Heat exchanger equation 2 (eqn 2)
U = Overall heat transfer coefficient
A = Surface area
LMTD = Logarithmic mean temperature difference
The Practical Heat Transfer Control is determined by the molecular thermodynamic interactions between the fluids flowing through the heat exchanger and the geometry of the heat exchanger itself.
The overall U value is calculated by an equation specific to the geometric configuration of a Heat Exchanger. It is a function derived using dimensionless numbers such as Reynolds Number (Re), Prandlt Number (Pr), along with fluid flow parameters. The overall U value is calculated over the total surface area A of the heat exchanger, across which the fluids exchange heat.
The log mean difference of the inlet and outlet temperatures (LMTD) of the hot and cold fluids for a counter flow exchanger is expressed by the formula:
Heat exchanger equation 3 (eqn 3)
Thi = Inlet temperature of hot fluid
Tco = Outlet temperature of cold fluid
Tho = Outlet temperature of hot fluid
Tci = Inlet temperature of cold fluid
Practical heat exchange value, Qp, can be compared to the theoretical, Qt, value to determine if the heat Exchanger has enough capacity to fulfill the application requirements.